Professionally Customize Automobile Motor
Recommended Supporting Suppliers for
Global First-tier OEMs
Industrial Product Supporting Capacity
Low Noise,High Quality,Safety, Low Energy Consumption
Industry Innovations
Dishwasher Dispenser Series
- Intelligent tips for a comfortable home life
- Reliable dispensing for the ultimate experience
- Highly adaptable to meet the diverse needs of users
- Modular design for easy operation
New Products for Automotive Air Conditioning Applications
Automotive Air Damper / Motorised Air Vent Actuator
- Miniaturised solutions, Smaller size, Meet the demand for lightweight automotive products
- Domestic chip, Stable supply, Maintain a certain price advantage
- Consistent size and performance, Can replace the imported product programme
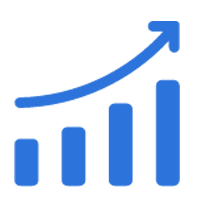
Founded in 1993
Stock code 300660
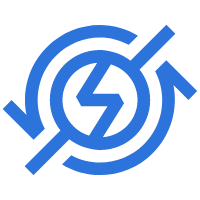
Qualification
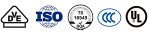
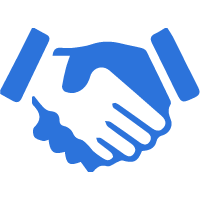
Professional customization
Annual production:200 million motors+
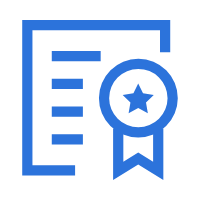
500+
World famous brand partner
Products and Applications
-
Home Appliance Market
Committed to providing innovative solutions for the global home appliance industry
- Leading brand in global air conditioning sweep motor market
- A global leader in washing machine drainage systems
- Global Refrigerator lce Water System Solution Provider
Home Appliance Market
Committed to providing innovative solutions for the global home appliance industry
- Customer Cases
- Specific Classfication
Air Conditioner
Refrigerator
Washing Machine
Kitchen & Bathroom
Small Home Appliances
-
Auto Parts
Provide motor and mechatronic components for automobiles
- Product advantages of stepper motors for HUD
- Large-scale automotive water pump production capacity
- Automotive air conditioning system solution capabilities
Auto Parts
Provide motor and mechatronic components for automobiles
- Customer Cases
- Specific Classfication
Air Conditioning System
Thermal Management
Intelligent Driving
Intake & Exhaust System
Body Control
Braking System
-
Industrial Control
Provide cost-effective motor and component products in the industrial field
- First-tier brand suppliers in the valve control market
- Domestic security monitoring head enterprise supplier
- Multiple series of products meet different application scenarios
Industrial Control
Provide cost-effective motor and component products in the industrial field
- Customer Cases
- Specific Classfication
Valve Control
OA Finances
Garden Tools
Industrial Equipment
Security Monitoring
Robot
-
Sports Health
Provide high-quality motors for sports equipment and medical equipment industries
- High-end sports equipment main drive motor supplier
- First-tier brand suppliers in the medical device industry
- Ability to provide solutions such as smart furniture
Sports Health
Provide high-quality motors for sports equipment and medical equipment industries
- Customer Cases
- Specific Classfication
Sports Equipment
Medical Instruments
Game Entertainment
Smart Home
Outer Diameter 20-50mm
Outer Diameter 6.5-60mm
Outer Diameter 35-60mm
Motors for Valve Control
Full Range of Brushless Types
Various Options Available
DC/AC Programme
Washing Machine Drain Pumps
Automotive Heat Management Pumps
Motors for Valve Control
New Products
- The industrial motor on the market is mainly AC high energy consumption, and the application of permanent magnet motor is less.
Rare Earth Removal Efficient
Permanent Magnet Synchronous Motor
More efficient and energy-saving than same-priced asynchronous motor.
Trending for Industrial Motor Development
- High efficiency, energy saving and green development
- Intelligent and integration
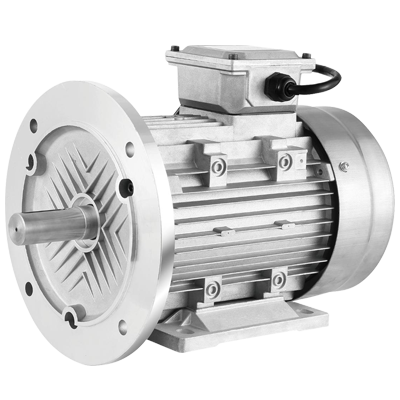
Self-developed Stator Soft Magnetic Material
- Strong plasticity, simple manufacturing process
- Energy saving, environmental protection, high strength
Self-developed Magnetic Rotor Material
- High dimensional stability
- Double permeability design, improve the motor full frequency high efficiency band
Integrated Design
- Small size, light weight
- Intelligent, low noise
- Domestic dishwasher penetration rate is low, the market demand has continued to increase in recent years, the market outlook is large.
Industry Innovative
Intelligent Dishwasher Dispenser
Multiple options for different types of detergents.
Dishwasher Development Trend
- High-end functional requirements
- Wider market prospects for embedded / single-use
- Dishwasher detergents towards integration and liquidisation
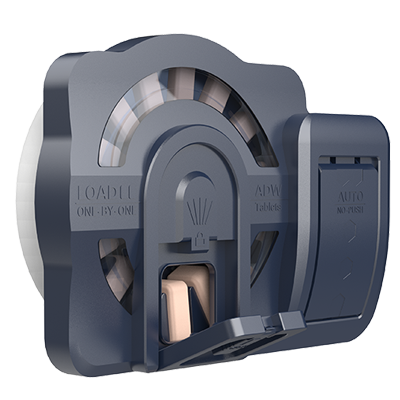
Highly Adaptable
- Four options to choose from
- Meets most of the dishwasher detergent dispensing needs on the market
Reliable Detergent Dispensing
- Reliable, active pushing out of the dishwasher block
- Liquid filling pump with good liquid viscosity adaptability
Modular Design
- Modular design, simple structure
- Plug-in installation of the dosing pump
- Increasing demand for automotive comfort, automotive air conditioning market trends towards electrification and intelligence.
Automotive Air Damper / Motorised Air Vent Actuator
Miniaturised solutions for lightweight requirements.
Automotive Air Conditioning Air Vents Market Trends
- Automotive air conditioning air vents electrification, intelligence
- Large air outlet area, wide-angle wind sweeping
- Require high efficiency and good stability of air vents
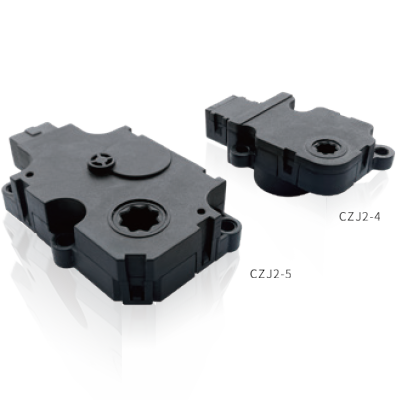
Product Lightweighting
- Miniaturised solutions with smaller dimensions
- Meet the demand for lightweight automotive products
Stable Supply
- Domestic chip, can provide stable supply
- Maintain a certain price advantage
Substitute for Imported Products
- Maintain the same size and performance
- There can be a substitute for imported products programme
Client Cooperation
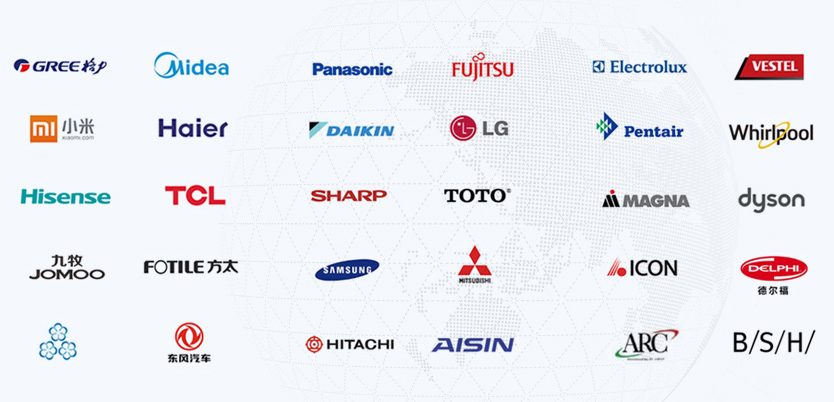
Providing you with a full range of CUSTOMISED SERVICES
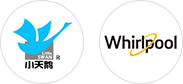
Relying on the application advantages and customer base in the drainage system of washing machines, Leili continues to meet the needs of new projects of customers and provide customized solutions for the functional requirements of high-end washing machines. After years of research and development, the automatic feeding system for washing machines has been mass-produced by customers such as Little Swan and Whirlpool.
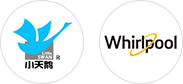
The application of Leili motor in refrigerator products is mainly synchronous motor. In recent years, the customer’s demand for refrigerator ice-making function, Leili motor and the customer close communication, collaborative research and development of refrigerator ice and water system components, for the customer to produce high-end refrigerator to provide assistance. At present, the refrigerator component products have been developed in series for different application scenarios of different customers such as Whirlpool, Midea and GE.
News Center
LEILI is excited to participate in the upcoming 137th Canton Fair, scheduled from April 15th to April 19th at the Canton Fair Complex, No.382, Yuejiang Zhong Road, Guangzhou. As a global leader in motion control and motor solutions, LEILI is excited to meet customers, partners, and visitors from around the world during this premier international trade event.
This spring session of the Canton Fair, known as China’s largest and most comprehensive trade fair, presents an invaluable opportunity for industry professionals to explore the latest trends, forge new connections, and discover cutting-edge products. At LEILI, we are proud to be part of this dynamic platform once again.
Visit LEILI at Booth No. 19.2E35-36, 19.2F13-14
We warmly welcome all attendees to visit us at our booth No. 19.2E35-36 and 19.2F13-14, where we will showcase our full portfolio of innovative motor products and intelligent drive systems. From precision micro motors to integrated motion control solutions, LEILI’s products are widely applied in smart home appliances, medical equipment, industrial automation, and automotive systems.
Visitors will have the chance to:
- Examine the introduction of new products with cutting-edge features and increased effectiveness.
- Experience live demonstrations of our motor solutions in action
- Engage with our professional team to discuss custom solutions for your application needs
- Discover LEILI’s latest R&D advancements in brushless motors, stepper motors, servo systems, and more
With over two decades of expertise and a strong commitment to innovation, LEILI continues to lead the way in delivering reliable, energy-efficient, and intelligent motor solutions to clients around the globe.
What to Expect at LEILI’s Booth
Our booth will highlight LEILI’s core technologies and product advantages. You’ll see:
- High-performance BLDC motors designed for smooth operation and high torque output
- Stepper motors and gear motors developed for precise positioning and quiet operation
- Advanced servo drive systems offering superior control for industrial automation
- Customized motor assemblies tailored to meet specific customer requirements
Our engineering and sales teams will be on-site, ready to provide in-depth technical support and one-on-one consultation. Whether you’re seeking a standard model or a fully customized solution, LEILI offers the flexibility and expertise to support your unique project.
Let’s Connect and Innovate Together
The Canton Fair is more than an exhibition — it’s a global meeting point for ideas, technology, and partnerships. At LEILI, we believe in the power of collaboration to create smarter and more sustainable motion solutions. We look forward to sharing our vision and learning from your insights.
Mark your calendar:
📅 Date: April 15–19, 2025
📍 Venue: Canton Fair Complex, No.382 Yuejiang Zhong Road, Guangzhou
🧭 Booth: 19.2E35-36, 19.2F13-14
Welcome to our booth — let’s shape the future of motion together!
A brushless direct current (DC) motor, also known as a synchronous electric motor, is driven by DC electricity instead of a mechanical commutation system. Brushless DC motors have high efficiency and reliability, help lower acoustic noise, and offer dynamic response, high speed range, and long durability, which are among the key features expected to leverage the brushless DC motor market growth.
Request For Sample Copy of this Research Report:https://www.coherentmarketinsights.com/insight/request-sample/1438
The higher efficiency of brushless DC motors in comparison with other induction or magnetic motors is driving the growth of the brushless DC motors market. Brushless DC motors are more efficient than their brushed DC counterparts, as it is associated with lower mechanical wear outs, thus lowering maintenance costs.
Brushless motor operates at low temperatures, require minimum maintenance, are thermally resistant, and remove any threat of sparks. This, in turn, has increased the demand for brushless motors over other types. Integration of sensor-less controls in brushless DC motors helps boost the durability and reliability of the product, in turn decreases the number of mechanical misalignment and electrical connections and reduces the weight and size of the product. The demand for the sensor-less controls from the industrial machinery has increased considerably due to its low cost and robust motor drives.
Among end users, the industrial automation equipment segment held the largest market share in the brushless DC motors market due to the growing demand for hybrid and electric cars. According to the International Energy Agency, in 2016, electric car sales were over 750 thousand worldwide. The consumer goods segment is rapidly growing due to increasing demand for heating, ventilation, and air conditioning (HVAC) technology, which in turn is increasing the demand for brushless DC motors.
Asia Pacific held the large brushless DC motors market share due to the rising production of electric cars and increasing demand for consumer electronics. According to the International Energy Agency, in 2016, China held the largest market share in the electric cars market, accounting for over 40% of the global electric cars sold.
The market in North America is expected to witness the fastest growth due to the growing demand for extremely sophisticated medical devices. For example, the development of positive airway pressure (PAP) breathing apparatus for the treatment of sleep apnea. This device, which helps patients in breathing also employs a brushless DC motor to power the blower fan.
Key players operating in the brushless DC motors market include Johnson Electric, Ametek, MinebeaMitsumi Inc., Allied Motion Technologies Inc., Maxon Motor AG, Emerson Electric Corporation, ABB, Nidec Corporation, and ARC Systems.
For More Information: https://www.coherentmarketinsights.com/ongoing-insight/brushless-dc-motors-market-1438
Another year of glorious blossoms in spring and solid fruits in autumn, let us forge ahead and open a new chapter. On November 26, 2024, the signing ceremony of the cooperation agreement “Research and Development of Six-Phase Brushless Motor and Controller with Torque Feedback” between Changzhou Leili Motor Technology Co., Ltd., a subsidiary of Jiangsu Leili, and Southeast University was successfully held at Motor Technology. Liu Xiaoyu, chairman of the Science and Technology Association of Changzhou Xinbei District and member of the Party Group of the District Science and Technology Office; Huang Yunkai, member of the Party Committee and deputy dean of the College of Electrical Engineering of Southeast University; and Jiang Zheng, deputy director of Longhutang Street of the district, attended the event.
At the ceremony, Su Da, Director General of Engine Technology, welcomed and thanked the visitors and stated that the signing of this industry-university research cooperation agreement marks a milestone in the more than 10 years of cooperation between the two sides, which will further boost cooperation. Engine Technology will continue to adhere to the principles of open cooperation and mutual benefit, and will explore new solutions and models with Southeast University in talent development, scientific research, and the transformation of achievements, jointly exploring the development of cutting-edge fields.
Huang Yunkai, Vice President of the College of Electrical Engineering at Southeast University, introduced the cooperation project and the university’s current research direction and held in-depth discussions with Mr. Su and the technical team. Liu Xiaoyu, President of the District Science and Technology Association, praised the cooperation between the College of Electrical Engineering and Southeast University. He noted that the government will provide policy support and guidance, and expressed his hope that the three parties—the college, the district, and the enterprise—will cooperate and promote technological innovation to a higher level. After the ceremony, Mr. Su led a delegation of guests to visit the company’s exhibition hall, introducing the company’s mature and outstanding products one by one and sharing future development plans.
We firmly believe that through close collaboration and collaborative efforts between schools and businesses, they can quickly meet the operational needs of intelligent driving in the new energy market and promote the development of new-level productivity. At the same time, both sides will actively explore new models of deep integration between industry, academia, and research, seeking to share resources and gain complementary advantages by cultivating high-quality innovative talent and creating high-level scientific research platforms, thereby boosting the competitiveness and social influence of enterprises.
Washing machines are vital household appliances, offering convenience, efficiency, and reliable cleaning performance worldwide. While most people are familiar with the drum, detergent drawer, and water inlet, the drain motor is one of the most important yet often overlooked components. Without it, dirty water would remain trapped in the tub, preventing the wash cycle from completing properly.
This guide explores how a drain motor works in washing machines, its components, working principles, maintenance tips, and troubleshooting techniques. Whether you are an appliance repair technician, an engineering student, or a curious homeowner, this article will give you a complete understanding of the drain motor’s role.
What is a Drain Motor in a Washing Machine?
The drain motor, also called the drain pump, expels dirty water from the washer after washing and rinsing cycles. It works in combination with the drain pump assembly, hoses, and control circuitry to ensure water flows out to the household drain system.
Key Functions:
- Removes dirty water after the wash cycle.
- Expels rinse water after the rinse phase.
- Prepares the tub for spinning by eliminating excess water.
- Prevents water stagnation that could cause odors or mold.
Types of Drain Motors
While the core function remains the same, drain motors vary depending on washing machine design and manufacturer.
Drain Motor Type | Description | Common Usage |
Synchronous AC Motor | Uses alternating current to drive the pump impeller at a fixed speed. | Common in front-load machines. |
Universal Motor | Operates on AC or DC, higher speed capability. | Found in some high-speed draining models. |
DC Brushless Motor | Uses electronic commutation for quiet and efficient operation. | Used in premium energy-efficient machines. |
Main Components of a Drain Motor System
Understanding the parts of a drain motor assembly is key to understanding its operation.
Motor Housing
Shields internal parts from water, dust, and physical damage to ensure reliable operation.
Rotor and Stator
- Rotor: The rotating component that drives the impeller.
- Stator: The stationary coil assembly that creates the magnetic field.
Impeller
A small fan-like structure connected to the rotor that pushes water through the drain hose.
Shaft Seal
Prevents water from leaking into the motor chamber.
Electrical Connector
Links the motor to the washing machine control board or timer.
Drain Pump Housing
Houses the impeller and channels water flow from the tub directly into the drain hose.
How a Drain Motor Works – Step-by-Step Process
Let’s explore the step-by-step operation of a washing machine drain motor during its cycle.
Step 1: Control Signal Activation
At the end of a wash or rinse cycle, the washing machine control board sends an electrical signal to the drain motor.
Step 2: Motor Rotation
The motor starts spinning the impeller, which generates a centrifugal force that moves water from the tub into the pump chamber.
Step 3: Water Movement
The spinning impeller pushes water into the drain hose, which is connected to the household drain pipe.
Step 4: Tub Emptying
The motor continues running until water level sensors or timers indicate the tub is empty.
Step 5: Automatic Shut-off
Once draining is complete, the motor stops to conserve energy and prepare for the next cycle.
The Science Behind the Drain Motor
Electromagnetic Operation
Most drain motors generate a rotating magnetic field via stator coils, which then drives the rotor to pump water.
Hydrodynamic Pumping
The impeller uses hydrodynamic principles to convert rotational energy into kinetic energy, pushing water out through the pump housing.
Synchronous vs. Asynchronous Operation
Synchronous motors maintain a fixed speed matching the power supply frequency.
Asynchronous motors can have slight speed variations depending on load.
Drain Motor in Different Washing Machine Types
Front-Load Washing Machines
Use high-efficiency AC drain motors.
Often incorporate filter traps to catch debris before it reaches the impeller.
Top-Load Washing Machines
May use simpler universal motors.
Pump assembly may be integrated into the transmission housing in older designs.
Compact or Portable Washers
Low-power DC motors enhance energy efficiency while ensuring quiet, smooth operation in washing machines.
Common Problems with Drain Motors
Problem | Possible Cause | Symptoms |
Motor not running | Electrical fault, blown fuse, faulty control board | Machine won’t drain |
Loud noise during draining | Damaged impeller, debris in pump housing | Grinding or rattling sound |
Slow draining | Clogged hose or filter | Water remains in tub after cycle |
Leaks | Worn shaft seal or cracked pump housing | Water under machine |
Maintenance Tips for Long Motor Life
Regularly clean the filter to avoid debris buildup.
Check drain hoses regularly for any kinks or blockages.
Run periodic cleaning cycles with descaling solution to prevent limescale buildup.
Avoid overloading the machine, which can cause excess strain on the motor.
Troubleshooting a Faulty Drain Motor
Safety First
Disconnect the washing machine from its electrical power source.
Turn off the washing machine’s main water supply.
Steps to Diagnose
- Check the Filter – Remove and clean any lint or debris.
- Inspect the Impeller – Check for any cracks, chips, blockages, or visible damage.
- Test Electrical Continuity – Check coil resistance using a multimeter for accurate measurement.
- Examine Wiring – Look for loose or corroded connectors.
Replacement
If the motor is faulty:
- Disconnect the wiring harness.
- Remove the mounting screws.
- Replace with a compatible OEM or high-quality aftermarket motor.
Energy Efficiency and Modern Innovations
Modern washing machines focus not only on effective water removal but also on energy savings and quiet operation.
Brushless DC Motors
Consume less electricity.
Operate with less vibration and noise.
Smart Control Integration
Variable-speed draining based on water load.
Self-diagnostic features to detect clogs or motor faults.
Eco-Drain Technology
Some premium washers reuse warm rinse water for the next wash cycle, requiring precise motor control to partially drain.
Comparing Drain Motor Designs
Feature | Synchronous AC | Universal | Brushless DC |
Efficiency | High | Moderate | Very high |
Noise | Low | Moderate | Very low |
Durability | High | Moderate | High |
Cost | Moderate | Low | High |
Lifespan of a Drain Motor
On average, a drain motor lasts 5–10 years, depending on:
- Usage frequency.
- Water quality (hard water shortens life).
- Maintenance practices.
Signs of end-of-life include frequent clogging, overheating, and increased noise.
The drain motor is a vital component that ensures your washing machine completes its cycles efficiently by removing water at the right times. Understanding how it works—along with proper maintenance and timely repairs—can extend its lifespan, improve washing machine performance, and prevent costly breakdowns.
Whether you’re dealing with a front-load, top-load, or portable washer, the drain motor’s operating principles remain largely the same: convert electrical energy into mechanical motion to pump water away from the tub. With the rise of energy-efficient brushless designs and smart diagnostic features, modern drain motors are becoming more reliable, quieter, and more sustainable than ever before.
Electronically Commutated (EC) centrifugal fans have become a preferred choice for HVAC systems, data centers, air handling units, and cleanroom environments due to their energy efficiency, precise speed control, and compact design. While these fans already offer quieter operation than many AC alternatives, noise reduction remains a critical engineering priority—especially in applications where comfort, productivity, or compliance with environmental noise regulations is essential.
Fan noise can affect human comfort, disrupt sensitive equipment, and even contribute to long-term hearing damage in high-intensity industrial environments. Therefore, integrating noise reduction technologies into EC centrifugal fan design is not just a performance enhancement—it is a necessity.
Noise Sources in EC Centrifugal Fans
Before applying noise control solutions, it is essential to first determine the sources of fan noise. In EC centrifugal fans, noise is typically categorized into aerodynamic, mechanical, and electrical sources.
Aerodynamic Noise
- Blade Passing Frequency (BPF): Caused by blades cutting through the air, creating pressure fluctuations.
- Turbulence: Generated by airflow separation, vortex shedding, and wake interactions.
- Inlet and Outlet Disturbances: Poor duct design can cause additional turbulence and noise.
Mechanical Noise
- Bearing Noise: Friction and imperfections in bearings generate vibration and tonal noise.
- Structural Resonance: Fan housings and mounts can amplify mechanical vibrations.
Electrical Noise
- Motor Commutation: Although EC motors use electronic commutation, switching transients can produce high-frequency tonal noise.
- Electromagnetic Vibration: Interaction between magnetic fields and rotor/stator components may cause audible hum.
Key Parameters Affecting Noise in EC Fans
Understanding the parameters influencing noise generation helps in selecting the right noise reduction strategies:
Parameter | Influence on Noise |
Blade Design | Shapes airflow, affects turbulence and tonal components |
Tip Clearance | Impacts vortex formation and high-frequency noise |
Fan Speed | Higher speed increases both tonal and broadband noise |
Housing Geometry | Poor design increases flow separation and turbulence |
Motor Control Method | Switching frequency impacts tonal electrical noise |
Aerodynamic Noise Reduction Technologies
Optimized Blade Profiles
Using airfoil-shaped blades reduces turbulence and increases aerodynamic efficiency. Today’s CFD technology enables engineers to:
Minimize stall points.
Reduce flow separation.
Smooth pressure gradients across the blade.
Example: Some EC centrifugal fans use backward-curved blades with optimized curvature to reduce vortex shedding.
Blade Count and Spacing Adjustments
Altering blade number changes the blade passing frequency, potentially moving tonal peaks away from sensitive frequency ranges.
Uneven blade spacing can spread noise energy across multiple frequencies, making it less perceptible.
Diffuser and Guide Vanes
Guide vanes straighten airflow after the impeller, reducing swirl and turbulence at the outlet. This minimizes broadband noise and improves static pressure recovery.
Inlet and Outlet Design Improvements
Bellmouth inlets smooth the air entry, reducing turbulence at the leading edge.
Flared or aerodynamic outlets help maintain laminar flow, lowering noise from sudden expansion.
Mechanical Noise Reduction Technologies
High-Precision Bearings
Low-noise, high-quality ball or sleeve bearings with optimized lubrication reduce friction-induced noise. Some EC fan manufacturers use ceramic hybrid bearings for lower vibration.
Vibration Isolation Mounts
Rubber, silicone, or spring mounts reduce structure-borne vibration transmission.
Particularly effective when fans are mounted in rigid HVAC frames.
Structural Damping
Applying damping materials (e.g., constrained layer damping sheets) to the fan housing reduces resonance amplification.
Electrical Noise Reduction Technologies
High-Switching-Frequency Drives
Increasing PWM (pulse-width modulation) switching frequency above the human audible range (>20 kHz) eliminates tonal switching noise.
Sinusoidal Commutation
Replacing traditional trapezoidal commutation with sinusoidal control smooths torque ripple, reducing both mechanical vibration and audible electrical hum.
Shielding and Filtering
Electromagnetic shielding and proper grounding reduce radiated electrical noise that can be picked up acoustically by other components.
Acoustic Treatment Technologies
Sound-Absorbing Materials
Acoustic foams inside the fan enclosure absorb high-frequency noise.
Fiberglass or mineral wool liners in ducts reduce broadband noise.
Silencers and Attenuators
Reactive silencers target tonal noise using resonators.
Dissipative silencers reduce broadband noise via absorption.
Enclosures and Acoustic Barriers
Placing fans inside an acoustic enclosure with soundproofing materials can drastically reduce radiated noise, though it must be balanced with cooling requirements.
Active Noise Control (ANC) in EC Fans
ANC systems use microphones, speakers, and digital processors to generate anti-phase sound waves that cancel unwanted noise. While more common in duct systems than individual fans, ANC can:
- Target specific tonal frequencies (e.g., blade passing frequency).
- Reduce low-frequency noise that passive materials struggle to absorb.
Control Strategy Optimization
Since EC motors offer precise speed control, intelligent fan speed management can be a noise reduction strategy:
- Variable Speed Operation: Reducing fan speed during low load periods decreases aerodynamic and mechanical noise.
- Soft Start/Stop: Gradual acceleration and deceleration reduce transient noise spikes.
- Load Matching: Avoiding operation near resonance frequencies improves overall noise performance.
Measurement and Validation
Noise reduction strategies must be verified through acoustic testing:
Test Type | Purpose |
Sound Power Level (SWL) | Determines total acoustic energy output |
Sound Pressure Level (SPL) | Measures perceived loudness at specific locations |
Frequency Spectrum Analysis | Identifies tonal peaks and broadband noise content |
Vibration Analysis | Detects mechanical resonance sources |
Testing should be conducted in accordance with ISO 3744 (free-field over a reflecting plane) or ISO 5136 (ducted fan noise measurement).
Real-World Application Examples
Case Study 1: Data Center Cooling
A large data center reduced cooling fan noise by:
- Switching from AC to EC centrifugal fans with backward-curved blades.
- Adding inlet bellmouths and duct silencers.
- Increasing PWM frequency to 25 kHz.
Result: 7 dB(A) noise reduction and improved cooling efficiency.
Case Study 2: Hospital HVAC
A hospital air handling unit integrated:
- Acoustic liners in ducts.
- Variable-speed EC fans with sinusoidal commutation.
- Vibration isolation mounts.
Result: Noise level in patient rooms dropped below 35 dB(A).
Comparative Effectiveness of Noise Reduction Methods
Noise Source | Technology Applied | Typical Reduction (dB) |
Aerodynamic | Optimized blade profile | 2–5 |
Aerodynamic | Inlet bellmouth + diffuser | 3–6 |
Mechanical | High-precision bearings + isolation | 2–4 |
Electrical | High-frequency PWM + sinusoidal control | 1–3 |
Acoustic | Silencers and duct liners | 5–10 |
Active | ANC (targeted tonal frequencies) | 5–15 |
Future Trends in EC Fan Noise Reduction
AI-Based Acoustic Optimization
Machine learning models can analyze real-time noise spectra and adjust fan speed, blade pitch (in variable-pitch designs), or ANC parameters dynamically.
Additive Manufacturing for Blade Design
3D printing allows highly complex blade geometries that improve aerodynamics and reduce turbulence.
Integrated Acoustic Sensors
Next-generation EC fans may include built-in microphones to monitor noise performance and trigger maintenance alerts continuously.
Noise reduction in EC centrifugal fans is achieved through a combination of aerodynamic optimization, mechanical isolation, electronic control refinement, and acoustic treatment. While each technology offers its own benefits, the most effective solutions combine multiple strategies tailored to the specific application.
By integrating noise control early in the design phase—and validating through standardized acoustic testing—manufacturers and system integrators can ensure that EC centrifugal fans deliver not only energy efficiency and reliability but also a quieter, more comfortable operating environment.
The global shift toward energy efficiency, precision control, and reduced maintenance costs has accelerated the adoption of Electronically Commutated (EC) centrifugal fans across industries. At the heart of these fans is the Brushless DC (BLDC) motor, a technology that merges the electrical efficiency of DC operation with the convenience of AC mains connectivity through integrated electronics.
While centrifugal fans have long been powered by traditional AC induction motors, the introduction of BLDC motors into fan design has transformed performance possibilities. EC centrifugal fans now offer superior energy efficiency, lower noise, precise airflow control, and extended service life—attributes directly linked to BLDC technology.
What is an EC Centrifugal Fan?
An EC centrifugal fan is a fan that uses a brushless DC motor powered by an integrated electronic control module. The “electronically commutated” part means that instead of using mechanical brushes and a commutator to switch current in the rotor windings, the switching is done electronically via a control circuit.
Key Points:
- Power Input: EC fans are connected to standard AC mains (single-phase 110–240V or three-phase 380–480V).
- Motor Operation: Internally, AC is rectified to DC and supplied to the BLDC motor windings.
- Speed Control: Controlled by pulse-width modulation (PWM), 0–10V analog signal, or digital protocols like Modbus or BACnet.
- Airflow Generation: The centrifugal impeller accelerates air radially outward, creating a pressure rise for ducted systems.
Inside the BLDC Motor
A Brushless DC motor inside an EC fan consists of:
- Stator – Laminated steel core with copper windings, forming the stationary part of the motor.
- Rotor – Permanent magnets mounted on a shaft, replacing rotor windings found in AC induction motors.
- Position Sensors – Detection of rotor position using Hall-effect sensors or through sensorless control algorithms.
- Electronic Controller (ECU) – Rectifies AC to DC, manages commutation, regulates speed, and controls torque.
Rotor
Uses rare-earth permanent magnets (typically NdFeB) for high magnetic flux density.
No rotor copper windings → eliminates rotor I²R losses.
Light rotor reduces rotational inertia for faster speed changes.
Stator
Wound with enamelled copper wire.
Optimized slot fill factor for higher efficiency.
Often designed with skewed slots to reduce cogging torque.
Commutation
Performed electronically rather than mechanically.
Switches current in windings in sync with rotor position to maintain torque production.
Two main methods: trapezoidal (block) commutation and sinusoidal commutation.
- Trapezoidal: Simple, good for cost-sensitive applications.
- Sinusoidal: Smoother torque, lower noise, ideal for HVAC fans.
How BLDC Motors Work in EC Fans
Power Conversion Path
- AC Input: From mains power supply.
- Rectification: AC is converted to DC using a diode bridge or rectifier.
- DC Bus: Filters and capacitors smooth DC voltage.
- Inverter Stage: High-speed switching (MOSFETs or IGBTs) generates 3-phase AC for the BLDC motor.
- Electronic Commutation: Controller adjusts phase timing based on rotor position feedback.
- Output Control: Matches fan speed to required airflow or pressure setpoint.
Why BLDC Motors Excel in EC Centrifugal Fans
Efficiency
BLDC motors achieve 80–90% efficiency compared to 60–75% for equivalent AC induction motors.
Reduced rotor losses and optimized winding design.
Speed Control
Smooth variable-speed control from 20% to 100% of rated speed.
High part-load efficiency—important for HVAC systems with variable airflow demands.
Noise Reduction
Sinusoidal commutation minimizes torque ripple.
Precise control reduces mechanical vibration and aerodynamic noise.
Compactness
Higher torque per volume allows smaller motors for the same output.
Eliminates bulky external VFDs by integrating control electronics.
Performance Comparison: AC Induction vs BLDC in Centrifugal Fans
Parameter | AC Induction Motor Fan | BLDC Motor EC Fan |
Motor Efficiency | 60–75% | 80–90% |
Speed Control Range | Limited without VFD | Wide (integrated control) |
Torque at Low Speed | Reduced | Maintained |
Heat Generation | Higher | Lower |
Noise Level | Higher at part load | Lower due to smoother commutation |
Maintenance | Bearings only | Bearings only |
Power Factor | 0.6–0.85 | >0.95 |
Design Considerations for BLDC Motors in EC Fans
Motor Sizing
Must handle peak torque during startup and transient load changes.
Oversizing slightly can improve thermal performance and extend lifespan.
Thermal Management
BLDC motors generate less heat, but integrated electronics require cooling.
Common methods: heat sinks on controller housing, forced airflow from impeller.
Magnet Selection
NdFeB offers highest performance but can lose magnetism at high temperatures (>150°C).
For high-heat applications, SmCo magnets may be used.
Control Algorithms
Field-Oriented Control (FOC) for optimal torque and efficiency.
Sensorless control for lower cost, but Hall sensors often preferred for high reliability in HVAC.
Integration with Fan Aerodynamics
BLDC motors enable new aerodynamic optimizations in EC centrifugal fans:
- Direct-drive design eliminates belts and pulleys, improving mechanical efficiency.
- Lower rotor inertia allows adaptive speed changes to meet real-time airflow demands.
- Integration with variable inlet vanes or EC impeller blades for peak performance.
Application
Commercial HVAC Systems
Fans for supply and return airflow in air handling units
Demand-controlled ventilation with CO₂ or occupancy sensors.
Data Centers
Precise temperature and pressure control for server room cooling.
EC fans integrated into Computer Room Air Conditioning units.
Refrigeration and Cooling Towers
Variable-speed fans reduce energy use during cooler ambient conditions.
Improved defrost cycles.
Cleanrooms & Laboratories
Low-noise, precision airflow for controlled environments.
Energy Savings Example
Consider a 5 kW centrifugal fan running 6,000 hours/year:
AC Induction Fan Efficiency: 70%
Input = 7.14 kW
Annual Energy Use = 42,840 kWh
BLDC EC Fan Efficiency: 88%
Input = 5.68 kW
Annual Energy Use = 34,080 kWh
Savings: 8,760 kWh/year (~$1,050/year at $0.12/kWh)
CO₂ Reduction: ~6.2 metric tons/year (based on 0.7 kg CO₂/kWh grid emission factor)
Reliability and Maintenance
No brushes → no brush wear, less downtime.
Bearings remain the only major wear component.
Electronics are designed for 40,000–60,000 hour lifespans but require protection from moisture and surges.
Industry Standards and Compliance
BLDC-powered EC fans often meet or exceed:
- EU ErP Directive for fan efficiency.
- US DOE Fan Energy Index (FEI) requirements.
- ISO 5801 (airflow performance testing).
- IEC 60034-30-2 for motor efficiency classification.
Future Trends
Wide Bandgap Semiconductors (SiC, GaN): Improve inverter efficiency and reduce controller size.
Sensorless High-Precision Control: For cost and reliability improvements.
IoT Integration: Remote monitoring, predictive maintenance, real-time optimization.
The Brushless DC motor is the technological backbone of EC centrifugal fans, delivering unmatched efficiency, control precision, and operational flexibility. By replacing mechanical commutation with electronics and integrating advanced motor control algorithms, BLDC motors enable fans to meet modern demands for energy savings, noise reduction, and adaptability.
When selecting centrifugal fans:
Choose BLDC EC fans for applications requiring variable speed, high efficiency, and precise control—such as HVAC, data centers, and clean environments.
Expect higher upfront costs, but significant lifecycle savings in energy and maintenance.
The industry trend is clear: as energy regulations tighten and technology costs fall, BLDC-powered EC centrifugal fans are set to become the new standard in air movement technology.
Centrifugal fans serve HVAC, industrial ventilation, clean rooms, electronics cooling, and various air-moving uses. They move air radially, changing its direction by 90 degrees and increasing its pressure. Traditionally, AC centrifugal fans—powered by alternating current induction motors—were the standard choice.
However, in the last decade, EC (Electronically Commutated) centrifugal fans, which integrate a brushless DC motor with onboard electronics, have emerged as a high-efficiency alternative.
Choosing between EC and AC centrifugal fans involves balancing performance, efficiency, cost, and application requirements. This article examines their differences in depth, providing data, examples, and recommendations.
AC Centrifugal Fans
- Driven by asynchronous induction motors powered directly from the AC mains.
- Speed is determined by supply frequency (50 Hz or 60 Hz) and motor pole count.
- Speed control requires additional devices (e.g., VFDs or voltage regulators).
Key Features:
- Simple, robust design.
- Long-established technology.
- Lower initial cost.
EC Centrifugal Fans
- Use brushless DC motors with integrated AC-to-DC conversion electronics.
- Speed control is built-in and managed electronically.
- Motor commutation is handled via microprocessor-controlled electronics.
Key Features:
- Higher efficiency.
- Integrated speed control.
- Precise airflow management.
How They Work
Feature | AC Centrifugal Fan | EC Centrifugal Fan |
Motor Type | Induction motor (single or three-phase) | Brushless DC motor with integrated electronics |
Power Supply | Direct AC | AC converted to DC internally |
Speed Control | External (VFD, voltage regulator) | Integrated electronic control |
Efficiency | 50–70% (typical) | 80–90% (typical) |
Maintenance | Minimal, but higher wear over long term | Very low, fewer wear parts |
Efficiency and Energy Consumption
AC centrifugal fans have limited efficiency due to:
- Rotor slip losses in induction motors.
- Fixed speed operation.
- Lower power factor at partial load.
- Use permanent magnets → no rotor slip losses.
- Operate with variable speed and optimized control algorithms.
- Provides excellent efficiency across a wide range of operating conditions.
Table 1: Typical Efficiency Comparison
Motor Power (kW) | AC Fan Efficiency (%) | EC Fan Efficiency (%) |
0.5 | 60 | 82 |
1.0 | 65 | 85 |
2.0 | 68 | 88 |
5.0 | 70 | 90 |
Energy Savings Example
Consider a 2 kW fan running 4,000 hours/year:
AC fan: 2 kW × 4,000 h ÷ 0.68 efficiency = 11,764 kWh/year
EC fan: 2 kW × 4,000 h ÷ 0.88 efficiency = 9,091 kWh/year
Annual Savings: 2,673 kWh/year, which could translate to $300–$500/year depending on electricity rates.
Speed Control and Airflow Management
AC Fans
Speed changes require frequency inverters (VFDs) or voltage controllers.
Each method adds cost and may introduce harmonic distortion.
Mechanical dampers are an option but waste energy.
EC Fans
Built-in electronic control allows speed adjustment via:
- 0–10V control signal
- PWM signal
- Modbus or BACnet communication
Allows dynamic adjustment for demand-based ventilation, leading to significant energy savings.
Noise Performance
- AC fans operate at fixed speed, often generating more noise during low demand periods since airflow cannot be reduced without throttling.
- EC fans reduce noise by slowing down during partial load, cutting sound levels significantly.
Table 2: Example Noise Levels
Operating Mode | AC Fan Noise (dB(A)) | EC Fan Noise (dB(A)) |
Full Speed | 75 | 74 |
70% Speed | 75 (throttled) | 66 |
50% Speed | 75 (throttled) | 60 |
Maintenance and Reliability
AC Fans
- Consistent performance under tough industrial conditions.
- Bearings require periodic inspection/lubrication.
- Motor winding insulation can degrade over decades.
EC Fans
- Fewer mechanical wear parts (no brushes).
- Electronics are the main wear point—quality design is crucial.
- Often have longer service intervals but can be more complex to repair.
Cost Considerations
Initial Purchase Cost
AC centrifugal fans: 20–40% lower upfront price.
EC centrifugal fans: Higher due to integrated electronics and permanent magnet motors.
Lifetime Cost
When factoring in energy savings and maintenance, EC fans often have a lower total cost of ownership (TCO).
Example ROI Calculation (2 kW fan):
- AC Fan Cost: $1,000
- EC Fan Cost: $1,400
- Annual Energy Savings: $350
- Payback Period: (1,400 – 1,000) ÷ 350 ≈ 1.14 years
Environmental Impact
EC fans contribute to:
Lower CO₂ emissions due to reduced energy use.
Compliance with efficiency regulations like EU Ecodesign Directive (ErP) or U.S. DOE fan efficiency rules.
Applications and Suitability
AC Fans: Best For
- Heavy-duty industrial settings where speed variation is not critical.
- Harsh environments where electronics may fail prematurely.
- Budget-sensitive projects.
EC Fans: Best For
- Commercial buildings requiring variable air volume (VAV) control.
- Data centers, cleanrooms, and laboratories where precise airflow is critical.
- Energy-efficient retrofits to meet green building standards.
Comparative Summary Table
Factor | AC Centrifugal Fan | EC Centrifugal Fan |
Efficiency | 50–70% | 80–90% |
Speed Control | External device required | Integrated |
Noise Control | Limited | Excellent at partial load |
Maintenance | Low to medium | Low |
Initial Cost | Low | Higher |
TCO | Higher (over lifetime) | Lower (energy savings) |
Best Use Case | Fixed-speed, industrial | Variable-speed, efficiency-driven |
Real-World Example: Data Center Ventilation Upgrade
A data center replaced 20 × 2 kW AC centrifugal fans with EC versions:
- Energy savings: 2,673 kWh/year/fan → 53,460 kWh/year total
- Annual cost savings: ~$8,000 (at $0.15/kWh)
- CO₂ reduction: ~25 metric tons/year
- Payback: 1.5 years
Decision-Making Framework
When choosing between EC and AC centrifugal fans, consider:
- Operating Hours – High operating hours favor EC fans for ROI.
- Airflow Variability – If demand fluctuates, EC offers more control and savings.
- Budget Constraints – AC may be better for short-term, low-cost installations.
- Environment – Harsh, high-temperature environments may still favor AC fans unless EC is specifically designed for such conditions.
- Regulatory Requirements – EC fans may be necessary to meet modern efficiency standards.
Both EC and AC centrifugal fans have valid applications:
AC fans remain reliable, cost-effective choices for fixed-speed, rugged industrial environments.
EC fans shine in energy efficiency, noise reduction, and precision airflow control, making them ideal for commercial, residential, and high-tech facilities.
If energy costs are significant and variable airflow is required, EC centrifugal fans almost always offer a better long-term investment. However, in cost-sensitive, fixed-speed industrial environments, AC centrifugal fans can still be the practical choice.